Enterprise PPM and DPMO
Digital Twin Use Case: Drive to Optimal PPM on a Global Scale
Bold corporate-level initiatives like driving towards zero PPM or DPMO require aggregation of data from various sources. This often results in an implementation of a common Digital Twin data model that scales across product lines, manufacturing locations, and supply chains. Supplier quality isn’t measured solely from supplier scorecards, incoming inspection, or inspection at the source. The quality of supplier parts needs to be gauged in manufacturing to see what is failing via PPM and DPMO. These metrics drive product quality and operational efficiency.
With real-time PPM and DPMO, electronics manufacturers can be alerted to emerging issues tied to rogue parts, supplier lots, supplier work orders, and more. If these issues are undetected, the OEM or CM can incur significant costs, quality issues, and operational inefficiency. By being able to proactively resolve quality issues, the manufacturer can improve product quality, prevent customer escapes as well as increase manufacturing velocity by decreasing the length and amount of rework cycles.
Digital Twin Use Case: PPM and DPMO
By deploying a manufacturing intelligence system with a common Digital Twin-based data model across all product lines, organizations can use this single source of truth for repeatable and trusted insights like PPM to optimize product quality, throughput and efficiency.
Challenge
- Automated detection/early warning for quality, supplier, and process issues
- Yield simulation of new designs
- Disparate data (ERP/MES/PLM/test)
- Supplier data is often in spreadsheets
- Data complexity
- Multi-level genealogy
- Change management
- Non-standardized attributes
- Manual investigation culture
- Accelerate root-cause investigation solution
Solution
- Purpose-built data model
- Fusion with Enterprise data
- BOM/ASSY/genealogy
- Repair/rework/test
- Attribute management
- Flexibility
- Off-the-shelf solution
- Continuously-supported
- Industry-hardened
- Pre-built measures and aggregations
- Pre-built analytics
- Customizable
- Automation
- Digital forms for manual capture
- Customizable
Benefits
- Enterprise-wide visibility
- Optimize product quality and throughput
- Maximize resource utilization
- Instant investigations into root-cause
- Collaboration with suppliers
- Accelerate time to market
- Accelerate time to value
A complete digital twin drives better manufacturing performance, quality, and outcomes. With IntraStage BlackBelt Fusion being the most complete version of the digital twin anywhere by making data analyzable and usable, contact us for a demo on how we can use our demo data or your actual manufacturing data to show you the power of the digital twin.
Heatmap Overlay
Rapid Root-Cause Identification and Resolution
OEE and Cycle Time
Improve Manufacturing Velocity and Productivity
As-Built, As-Maintained, As-Is
Full Traceability and Genealogy
Get the FREE TRIAL
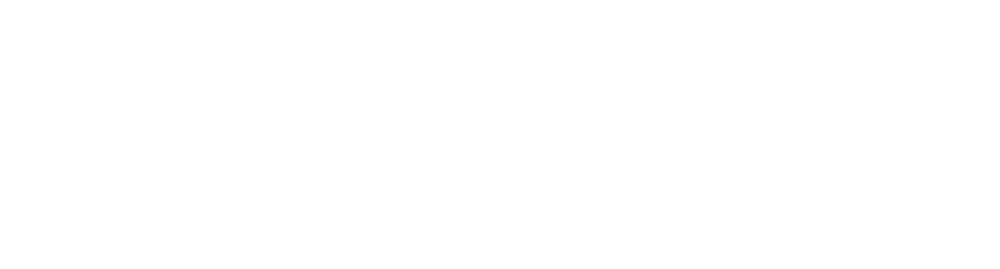