The Digital Thread for Complex Electronics Manufacturers
Solve
On-Demand Access To the Parametric Data That Drives Issue Investigation
Manage
Control The Processes that Define Quality and Profitability
Anticipate
Predict emerging issues by learning from previous issues
Recommend
Track the best performing resolutions, and apply those to future issues
Track
Gain confidence in your ability
Discover the Benefits
The BlackBelt Manufacturing suite is the core product platform integrating all IntraStage solutions in a single interface. The BlackBelt suite is designed to automate the capture, retrieval, storage, reporting and visualization of product manufacturing and quality data. By tying together the parametric-level data that is the digital thread that ties together manufacturing, supplier quality, returned materials authorization/RMA, R&D and Repair.
Products
BlackBelt Analytics Product Details
Designing, manufacturing and improving a highly complex electronic product requires analytics from anywhere or any testing fixture on the manufacturing line. By analyzing their data, IntraStage customers are reducing manufacturing costs through improved yield, reduced scrap and fewer quality escapes. Normalizing and databasing disparate datasets (whether they be R&D waveforms or Manufacturing ICT tester output or JTAG files) allows our off-the-shelf BlackBelt reports to be used, shared, and used for improvement. With built in analytics such as SPC Analytics (including Cp and Cpk, X-BarR, and Box and Whiskers charts), Gage R&R studies and detailed drill-downs allow your engineers to identify any factors affecting product yield, scrap, rework, and other factors before they affect product quality, users can quickly get to the information that matters.
Full Product Genealogy
Connect the Digital Thread of Performance
Predictive and Prescriptive
Track and Prevent Emerging Issues
On-Demand Parametric Performance
Track and Control the Data That Drives Quality and Improvement
Optional Add-ons Include
Failure Analysis Product Details
Any complex manufacturing environment has silos of the Hidden Factory. The Hidden Factory, where un-tracked repairs and rework are conducted on the manufacturing line, is a key factor in process and quality improvement. The IntraStage Failure Analysis software automates and tracks the workflow and data for repair and rework actions, bringing to light such key analytics as Mean Time Between Failures/MTBF, Failure Codes, rework details, and rework procedures for parent and child assemblies. By tracking and managing this kind of critical performance and quality data, nascent quality issues can be caught and tracked before they become line-stopping issues.
Rework and Repair Capture
Customizable Workflows to Capture the Rework and Repair Data Critical to Process Improvement
Predictive and Prescriptive
Track and Prevent Emerging Issues
Customizable Processes for the Factory Of the Future
Drive and Automate the Failure Analysis Process
Supplier and CM Quality Management Product Details
A quality issue in a batch of supplier parts can mean shortages on the line, or even a production stoppage. Or worse, a quality change in the supplier might result in more subtle changes that escape existing final tests. Collaboration between OEMs, CMs and Suppliers allows you to optimize the quality of your worldwide manufacturing chain. IntraStage customers are able to see real-time information on supplier quality through inspection at the source. Supplier Management personnel and their suppliers can identify marginal or failing components (including performance of measurement values against spec and control limits) and address quality issues even before they arrive at the incoming dock at your assembly factory.
Inspection At the Source
Capture Data Manually or Automatically at the Supplier
Predictive and Prescriptive
Track and Prevent Emerging Issues
Customizable Processes for the Factory Of the Future
Drive and Automate the Failure Analysis Process
Return Analysis Product Details
Existing RMA systems capture the logistics of returned materials, but what about the root cause? Which lots or batches provided a part that caused a disproportionate number of Returns? Which board revision is having a disproportionate number of early field failures? IntraStage customers are able to track the workflow of RMAs and manufacturing parts flagged for RMA to understand why their products are having field failures. An RMA manager who is focused on reducing customer returns needs to be able to quickly identify trends and actionable information derived from their RMA and Field Return data. By being able to correlate Field Quality Data metrics (like mean time between Failure), Field returns can have a dramatic effect on a product line’s profitability and brand reputation. The ability to tie field failures to original manufacturing and supplier test data helps our customers to quickly address quality issues.
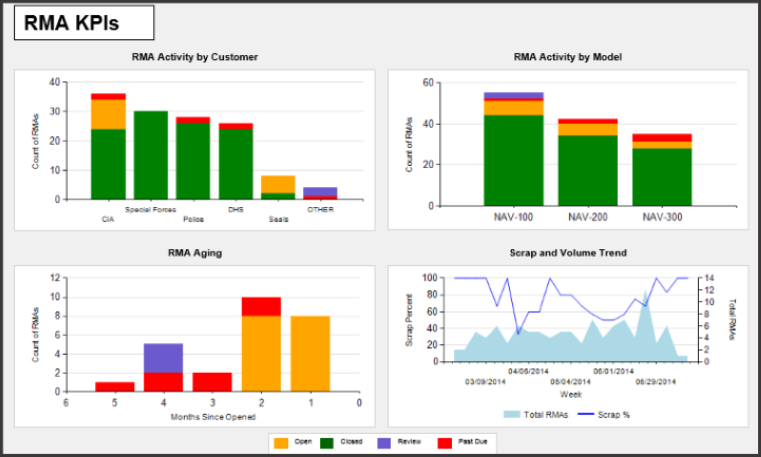
Manage
A quality issue, whether it root-caused to be from supplier parts, design, manufacturing process fidelity, can mean production line stoppages or even recalls.. IntraStage customers are able to see real-time information on their key quality metrics and track and manage quality issues before negative events occur.
Solve
The BlackBelt Manufacturing suite is the core product platform integrating all IntraStage solutions in a single interface. The BlackBelt suite is designed to automate the capture, retrieval, storage, reporting and visualization of product manufacturing and quality data. By tying together the parametric-level data that is the digital thread that ties together manufacturing, supplier quality, returned materials authorization/RMA, R&D and Repair.
Anticipate
Existing RMA systems capture the logistics of returned materials, but what about the root cause? Which lots or batches provided a part that caused a disproportionate number of Returns? Which board revision is having a disproportionate number of early field failures? IntraStage customers are able to track the workflow of RMAs and manufacturing parts flagged for RMA to understand why their products are having field failures. An RMA manager who is focused on reducing customer returns needs to be able to quickly identify trends and actionable information derived from their RMA and Field Return data. By being able to correlate Field Quality Data metrics (like mean time between Failure), Field returns can have a dramatic effect on a product line’s profitability and brand reputation. The ability to tie field failures to original manufacturing and supplier test data helps our customers to quickly address quality issues.
Recommend
Track
Existing RMA systems capture the logistics of returned materials, but what about the root cause? Which lots or batches provided a part that caused a disproportionate number of Returns? Which board revision is having a disproportionate number of early field failures? IntraStage customers are able to track the workflow of RMAs and manufacturing parts flagged for RMA to understand why their products are having field failures. An RMA manager who is focused on reducing customer returns needs to be able to quickly identify trends and actionable information derived from their RMA and Field Return data. By being able to correlate Field Quality Data metrics (like mean time between Failure), Field returns can have a dramatic effect on a product line’s profitability and brand reputation. The ability to tie field failures to original manufacturing and supplier test data helps our customers to quickly address quality issues.